Технология компактирования порошков
В условиях высокой конкуренции на рынке производства готовых лекарственных средств, разработки новых рецептур, фармацевтическим компаниям приходится искать нетривиальные решения для оптимизации производственного процесса, повышения качества и снижения себестоимости продукции.
Технология компактирования (сухого гранулирования) порошков это одно из возможных решений такого уровня задач фармацевтического производства.
Помимо экономического эффекта компактирование может быть возможным способом гранулирования для некоторых продуктов, при производстве которых не применим традиционный метод влажной грануляции.
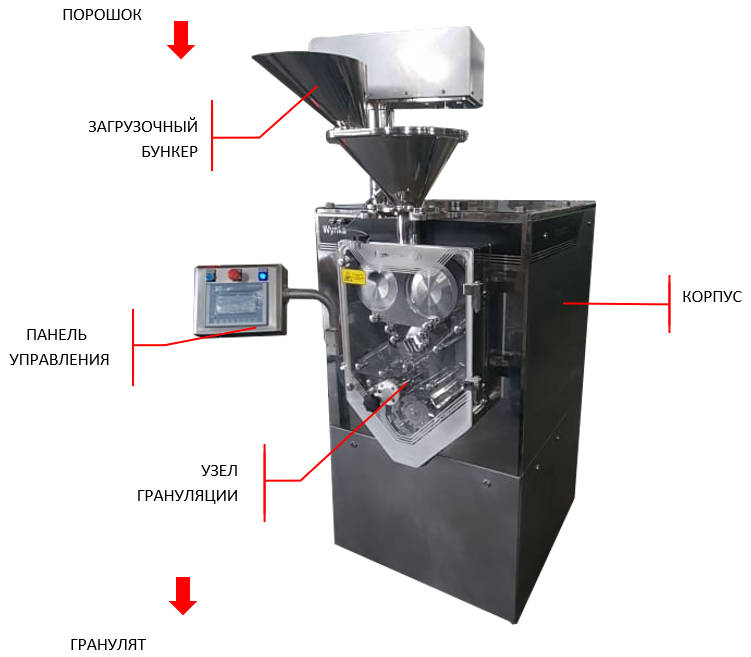
Сравнение работы машин на порошке и грануляте
В зависимости от типа твердых лекарственных форм для их производства может использоваться либо порошок, либо гранулят.
Работа с промежуточным продуктом в форме порошка связана с определенными трудностями. Это прежде всего повышенное пыление в производственной зоне, что несет в себе риски для персонала, продукта и оборудования. Оставим вопрос защиты персонала и перекрестной контаминации вне рамок данной статьи и рассмотрим только влияние выбора типа полупродукта (порошок или гранулят) на надежность работы технологического оборудования.
Традиционно для снижения себестоимости продукции, либо в случае невозможности использования влажной грануляции (типы таких продуктов будут рассмотрены ниже) используется прямое прессование на таблетпрессах и заполнение капсул/саше порошком. По сравнению с использованием гранулята, таблетпрессы, капсульные и саше машины работают с порошком на более низкой скорости (т.е. при меньшей производительности), наблюдается нестабильный вес финального продукта. Помимо этого, существенно повышается риск повреждения оборудования за счёт попадания мелкодисперсных частиц порошка в движущиеся части машин, что особенно критично для дорогостоящего пресс-инструмента и подвижных частей шнековых дозаторов. Самые частые проблемы в работе оборудования на порошке – это заклинивание и затирание пресс-инструмента и шнека, некорректная работа узла ориентации и закрытия капсул, брак запайки саше.
Использование компактора в технологической схеме решает обозначенные выше проблемы. Продукт после компактора можно направлять непосредственно на таблетпресс, капсульную или упаковочную машину.
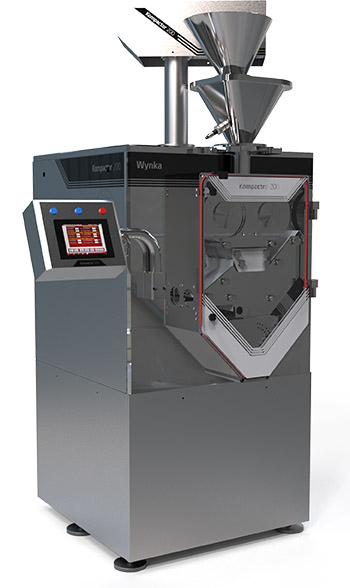
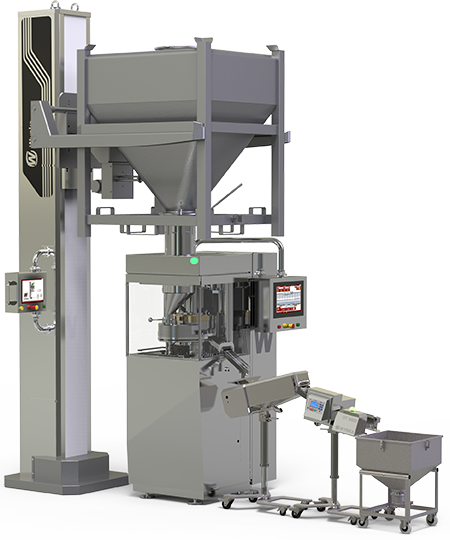
Применение технологии компактирования
Компактирование – это чрезвычайно экономически эффективная технология гранулирования, которая не требует установки габаритного и дорогостоящего оборудования, такого как миксер с высоким усилием сдвига и сушка в псевдоожиженном слое.
Технология компактирования решает задачи гранулирования для продуктов, которые не могут быть получены традиционным методом из-за сильного поглощения влаги или негативного влияния связующего вещества на качество продукта.
Если для продукта возможно использовать оба метода гранулирования, как сухое, так и влажное – компактирование технически проще и существенно ниже по стоимости.
Данная технология широко применяется для продуктов, содержащих в своем составе:
- гигроскопические материалы;
- термолабильные материалы;
- активные вещества, разлагающиеся в воде;
- вещества, обладающие хорошей прессуемостью, без необходимости связывания частиц раствором.
Для того, чтобы порошок мог быть способен гранулироваться сухим методом (с использованием компактора), он должен обладать внутренними свойствами уплотнения, возможностью связать частицы вместе. Чем лучше прессуемость продукта – тем меньше требуется давление и тем выше скорость вращения роликов и, соответственно, выше производительность машины. Для данной технологии большое влияние оказывает состав порошка и выбор сухого связующего вещества в рецептуре. Прессуемость порошка можно улучшить за счет добавления сухих связующих веществ. Концентрация сухих связующих веществ оказывает влияние на необходимое для компактирование усилие сжатие, что в свою очередь определяет максимально возможную производительность для получения гранулята заданного качества.
С помощью компактирования решаются следующие задачи:
- снижение пыления;
- улучшение подачи и дозирования продукта;
- повышение однородности распределения активного компонента в смеси;
- увеличение плотности порошков с изначально низкой плотностью;
- увеличение размера частиц и как следствие, сыпучести смеси;
- увеличение производительности таблетпрессов;
- снижение риска поломки оборудования;
- снижение затрат на грануляцию;
- гибкий диапазон размера серии за счёт непрерывности процесса.
Устройство и принцип работы компактора
Порошок загружается в бункер машины. С помощью шнекового питателя порошок равномерно поступает на ролики и раскатывается в пластины. Расстояние между роликами регулируется и поддерживается автоматически таким образом, чтобы компенсировать колебательные силы, возникающие при сжатии, что обеспечивает сохранность узлов машины и однородность качества продукта. Рисунок роликов выбирается исходя из необходимого диапазона требуемых характеристик продукта.
Спрессованный в пластины продукт подается на измельчитель, который находится под узлом компактирования. Заданный размер гранул обеспечивает размер металлической решетки. Готовый продукт собирается в контейнер.
Минимальное расстояние между элементами системы обеспечивает низкое пыление в рабочую зону и снижение загрязнения узлов машины.
Архитектура машин данного типа предполагает, что процесс компактирования визуально легко контролируется оператором.
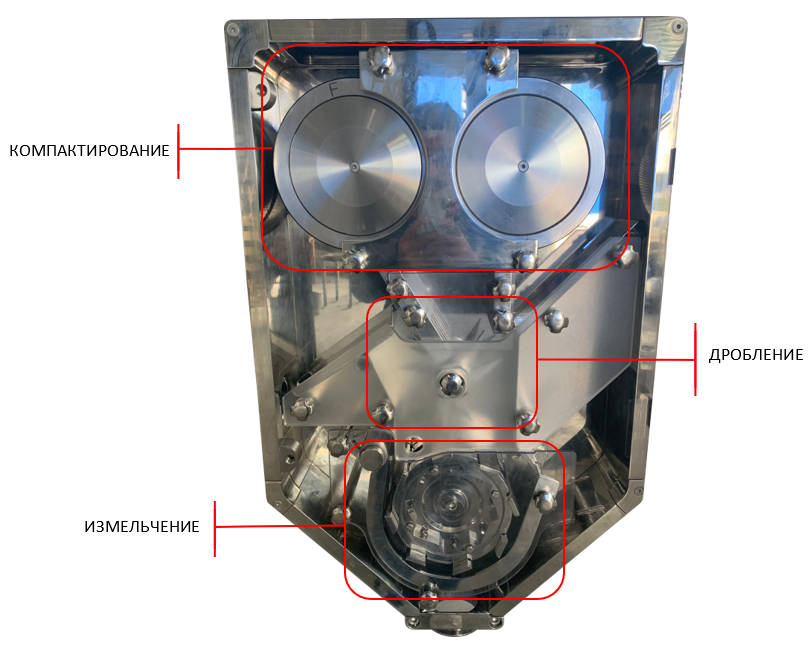

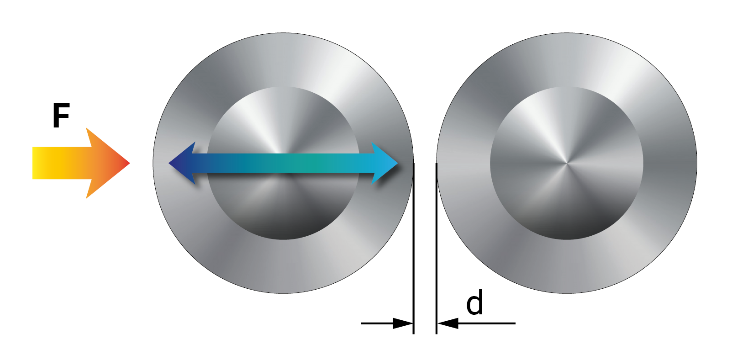
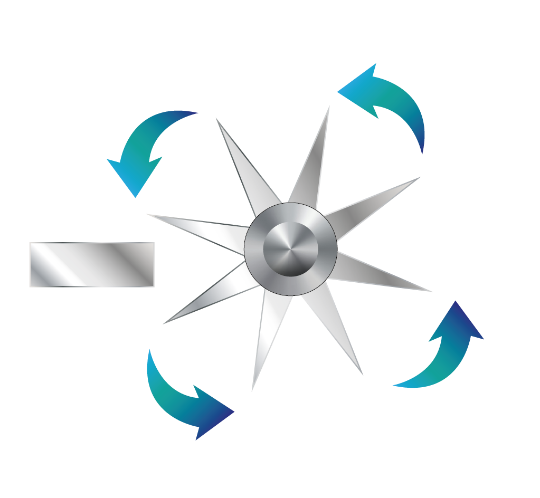
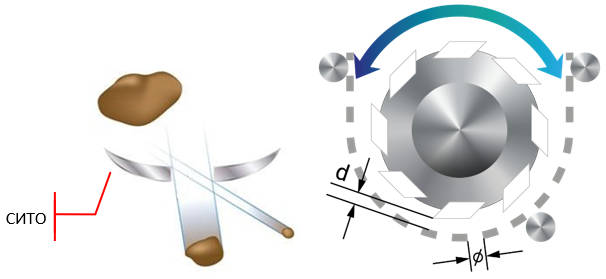
Сравнение компактирования с традиционной грануляцией
Параметры гранулята, получаемого при помощи компактирования и традиционной технологии влажного гранулирования отличаются. Гранулят, полученный при помощи компактирования, более плотный. При правильной конструкции оборудования и организации процесса содержание мелкой фракции минимизировано и может быть сопоставимо с классической технологией грануляции, крупные включения отсутствуют.
На свойство гранулята, полученного в установке псевдоожиженного слоя, главным образом влияет количество и режим подачи связующего вещества из распылительных форсунок. Данная технология позволяет получать гранулят однородного гранулометрического состава и снизить необходимое усилие прессования для таблетирования.
При компактировании есть возможность для регулировки параметров получаемого гранулята, которая достигается за счёт выбора расстояния между роликами и усилия сжатия, рисунка поверхности роликов, размера сетки, регулировки положения измельчителя и т.д.
Принятие решения о выборе технологии грануляции перед таблетированием должно быть основано на допустимом качестве таблетмассы для получения стабильной таблетки, соответствия допускам по плотности, прочности и массе.
Основные отличия сухого и влажного гранулирования:
- площадь для установки в 3-5 раз меньше;
- не требуется оборудование воздухоподготовки и подвод коммуникаций из технической зоны;
- энергозатраты на получение 1кг гранулята в 5-10 раз ниже;
- гибкий размер серии;
- проще в эксплуатации и обслуживании;
- ниже стоимость.